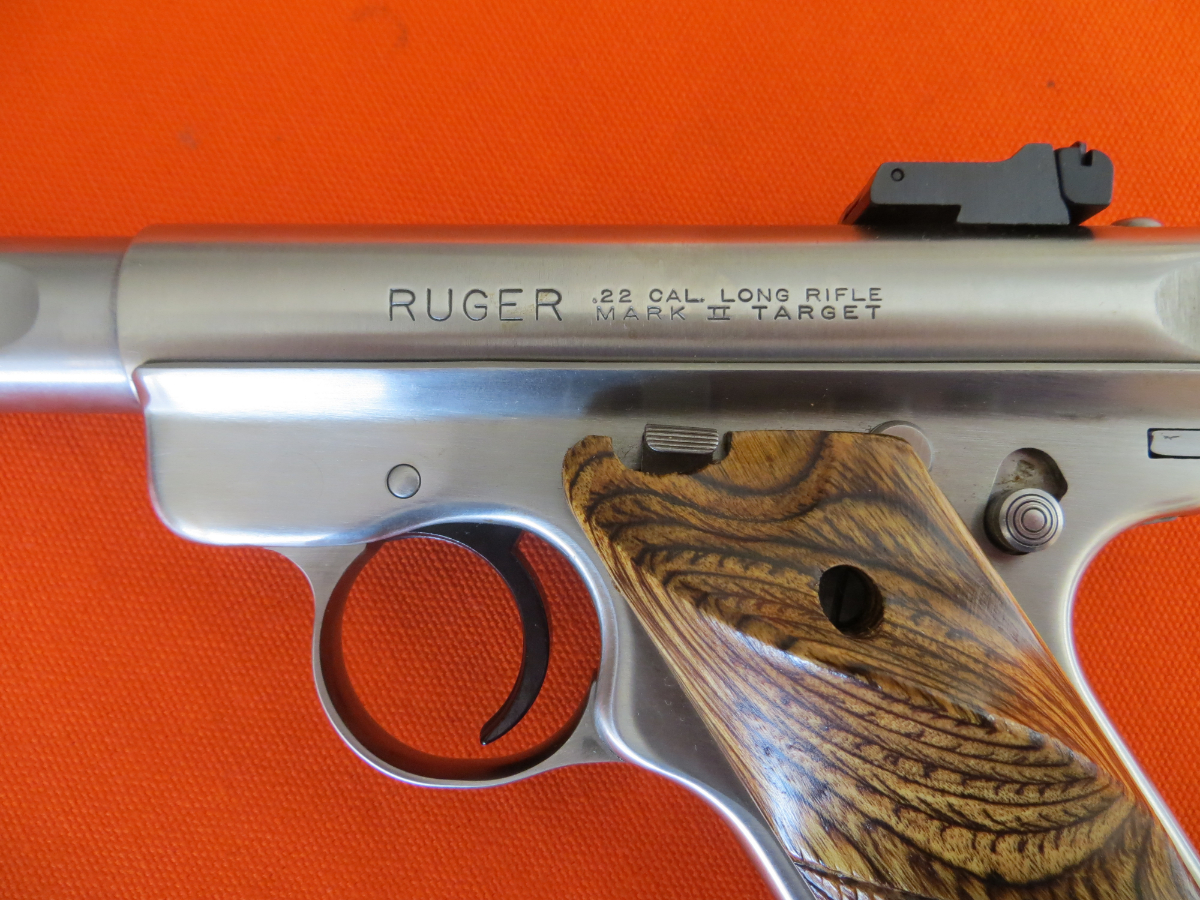
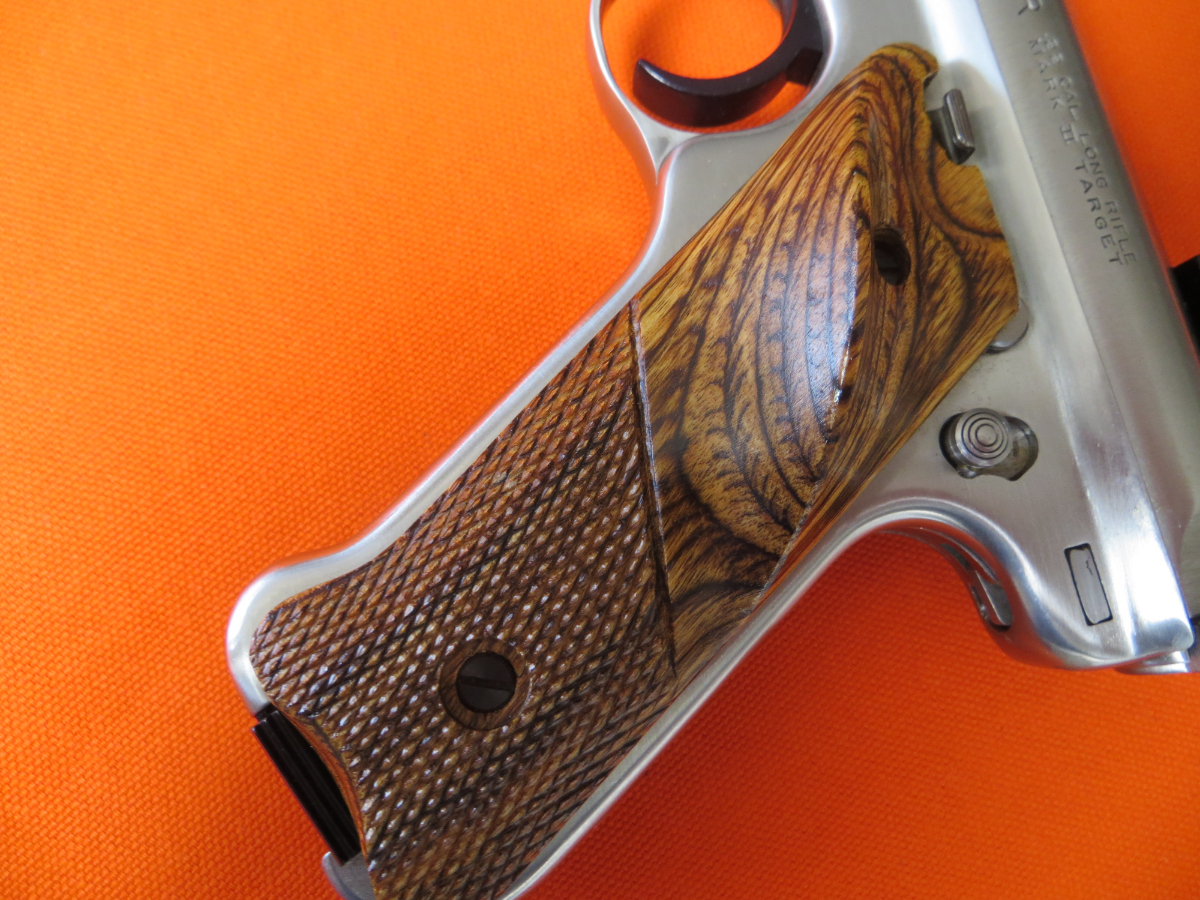
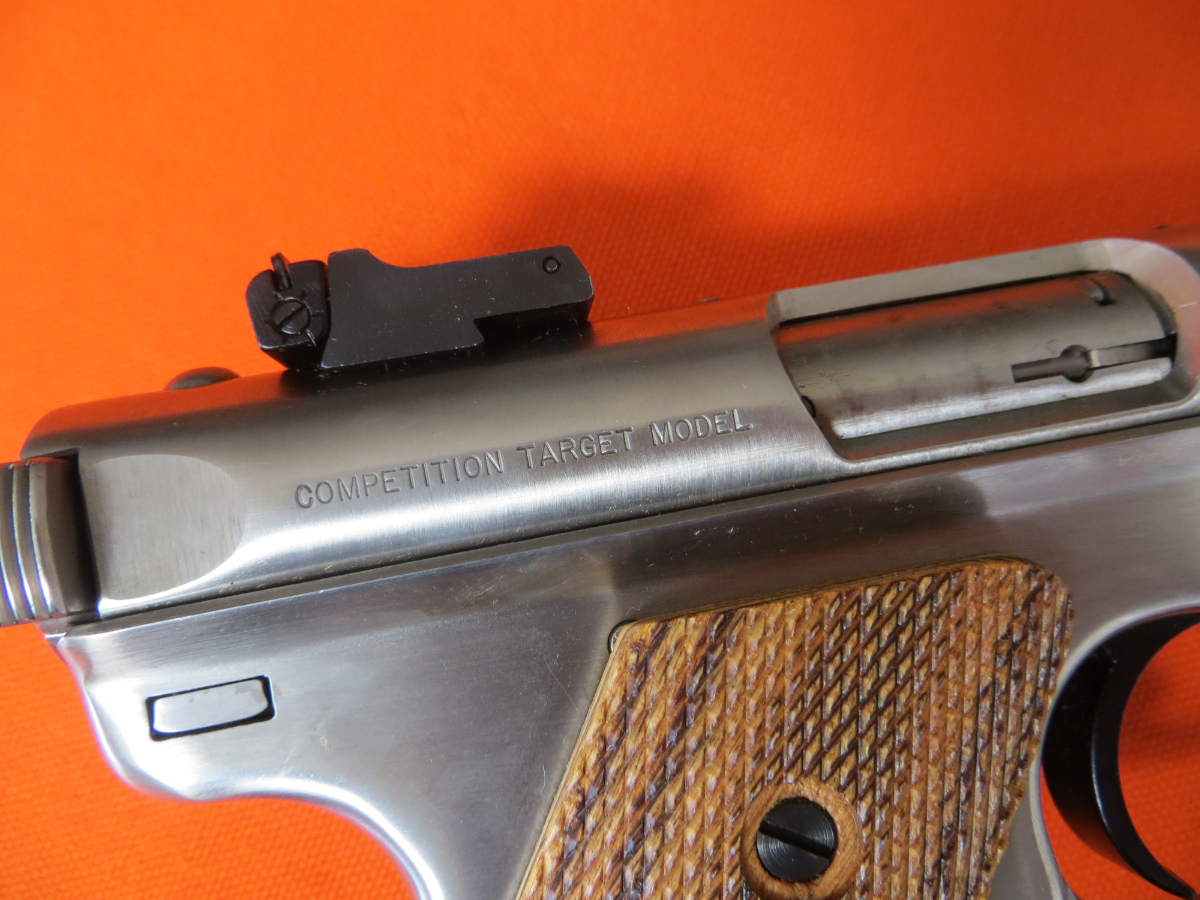
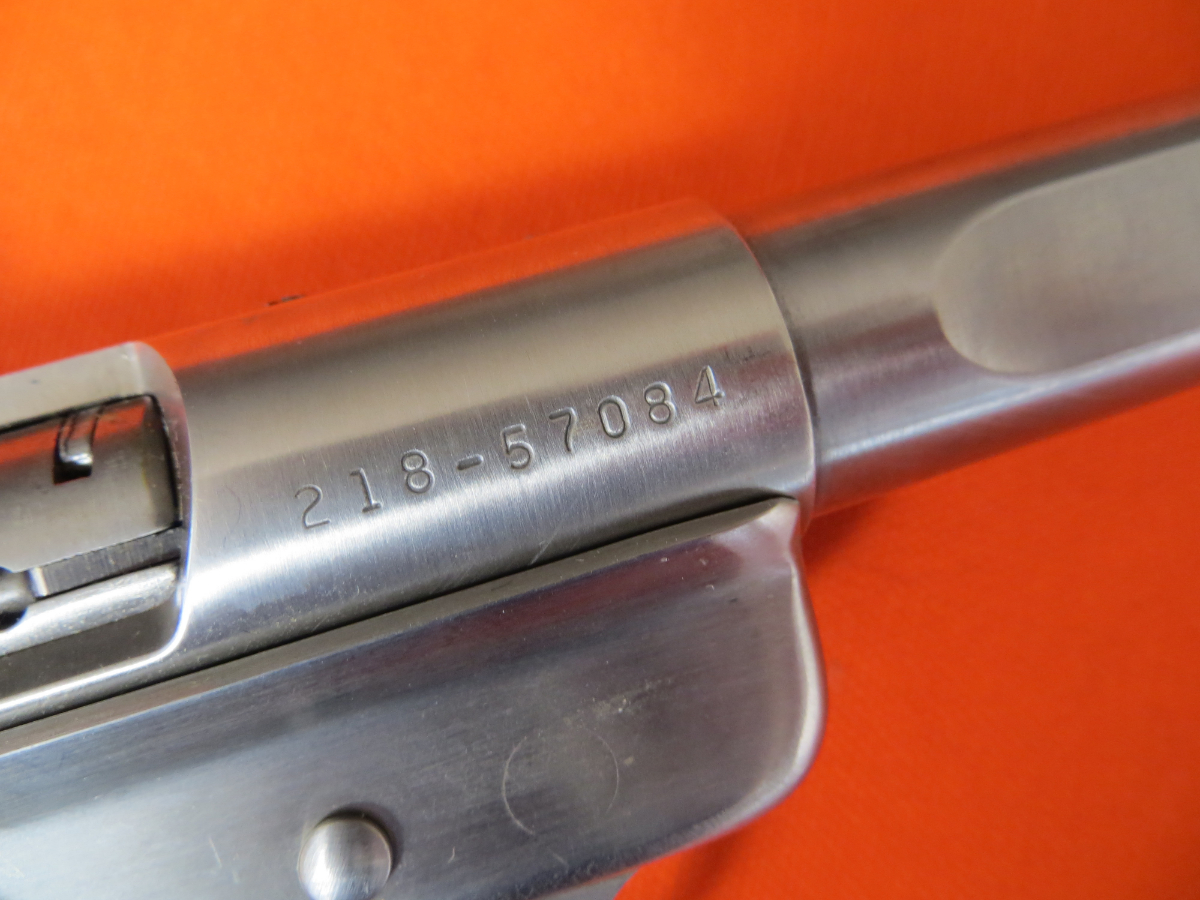
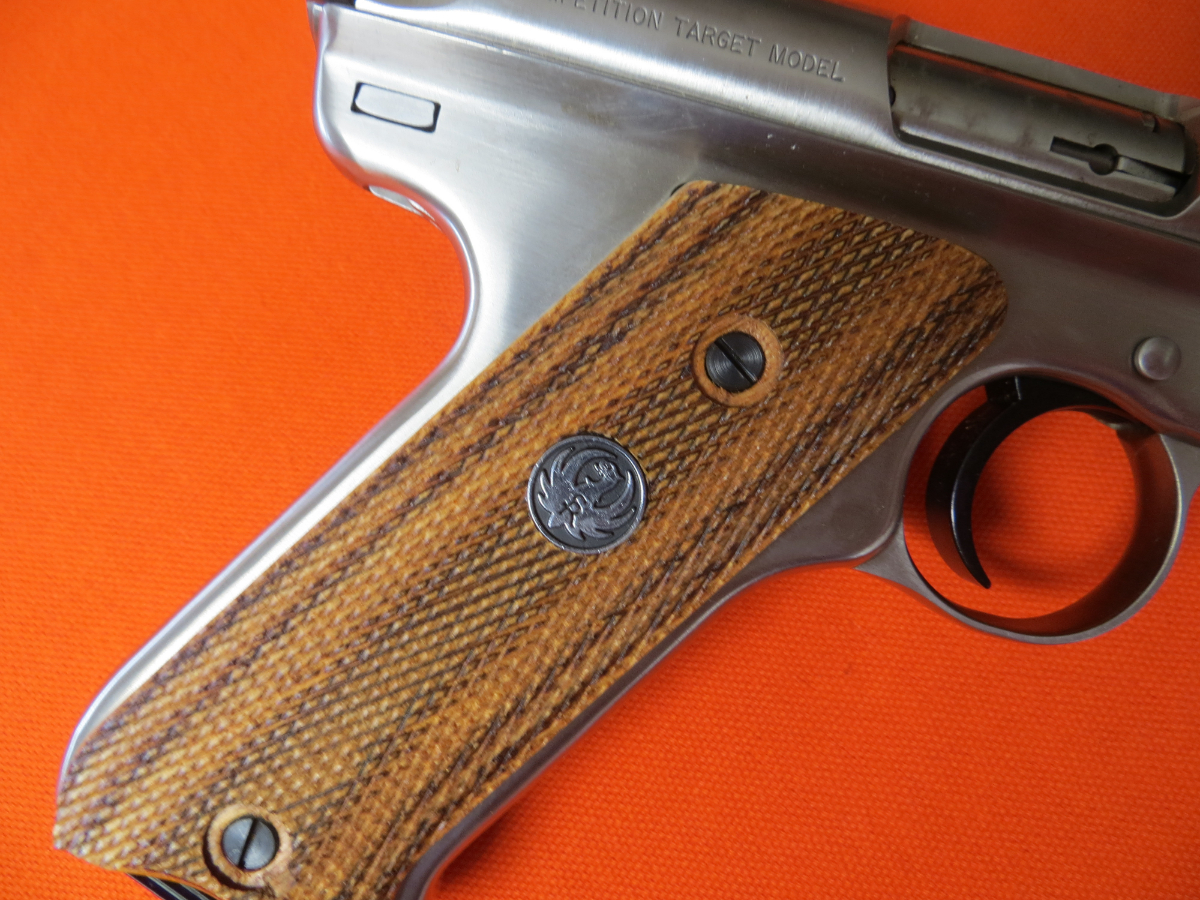
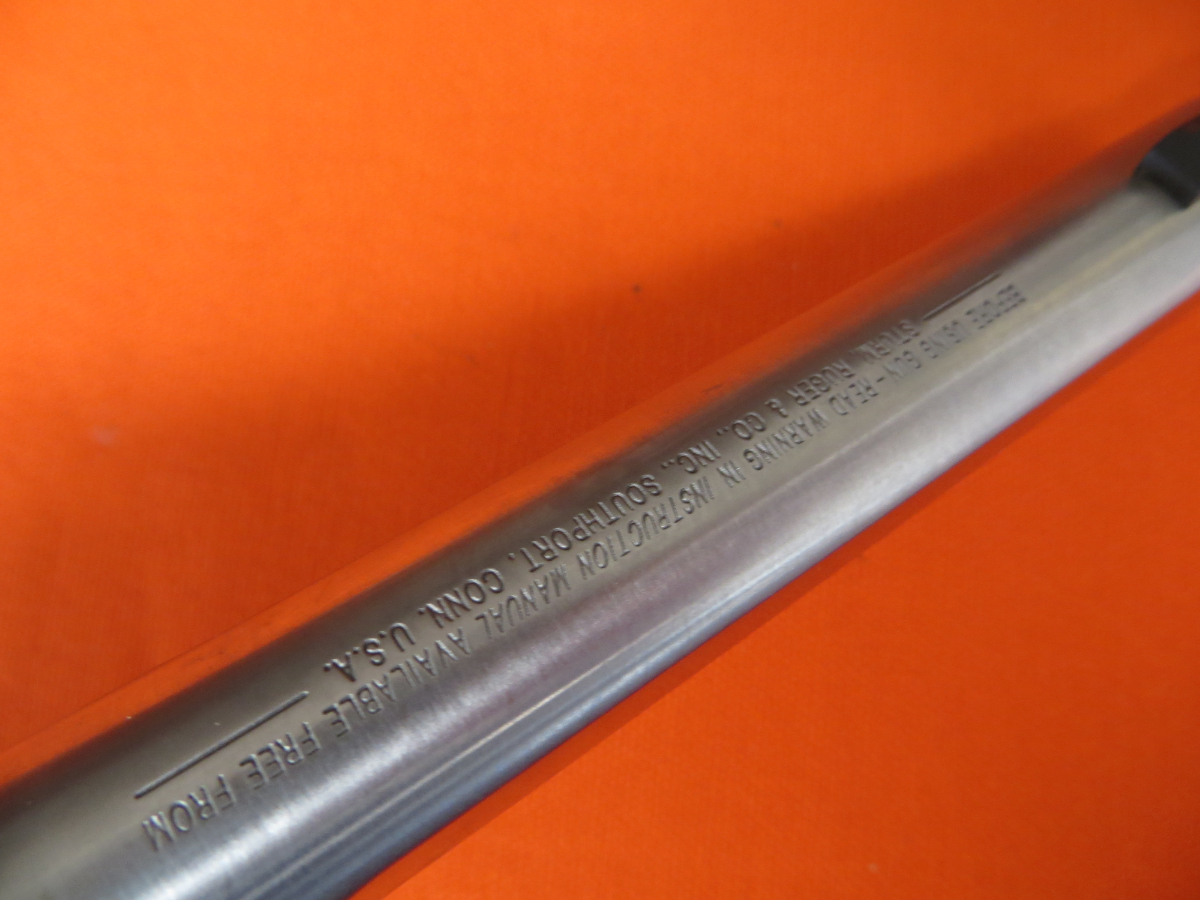
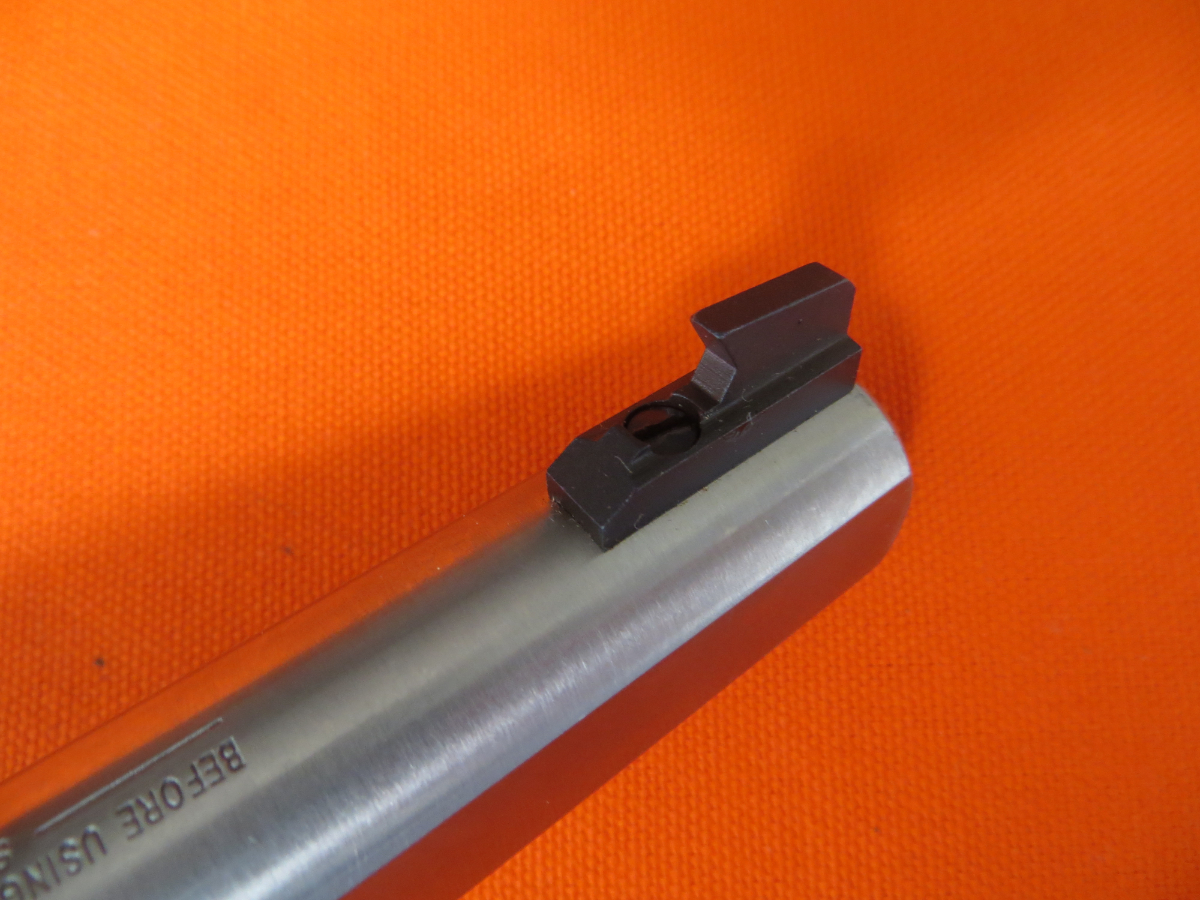
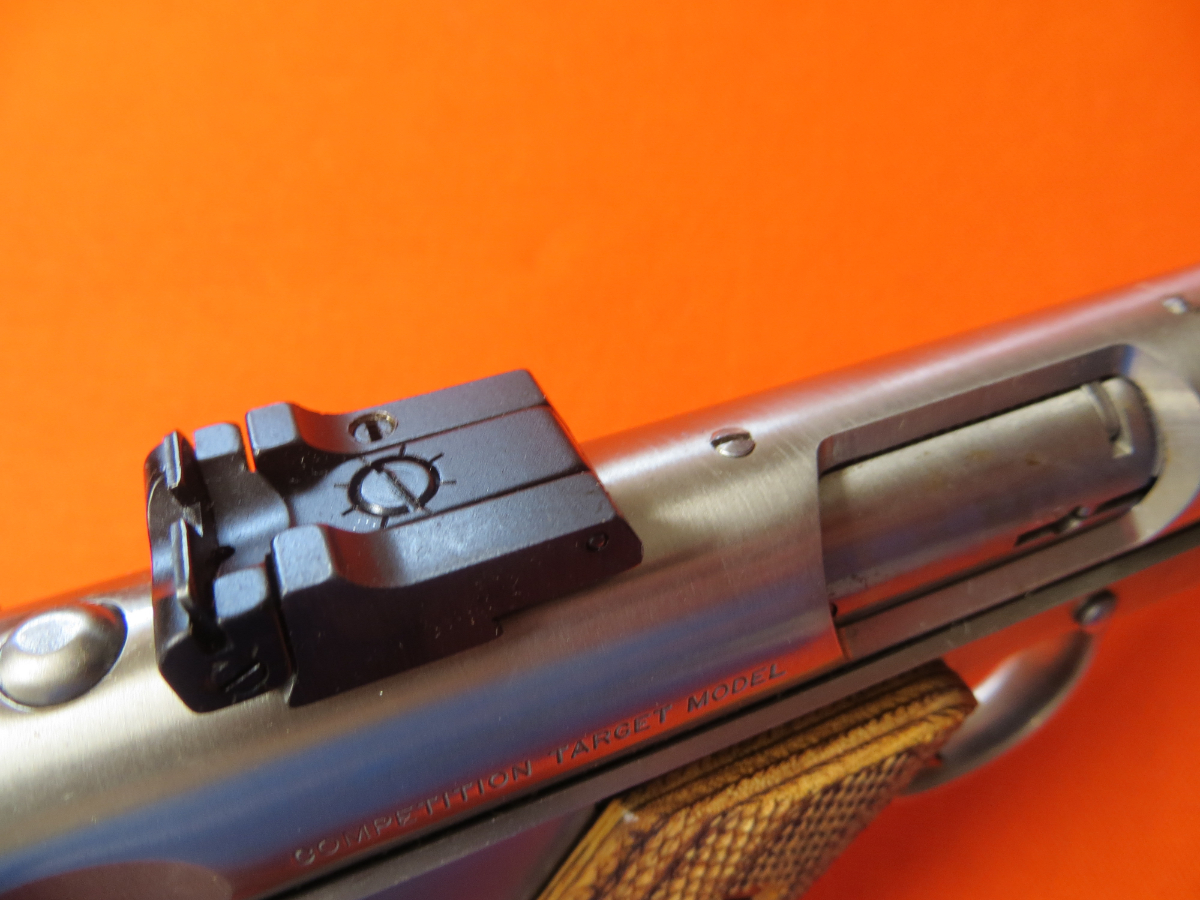
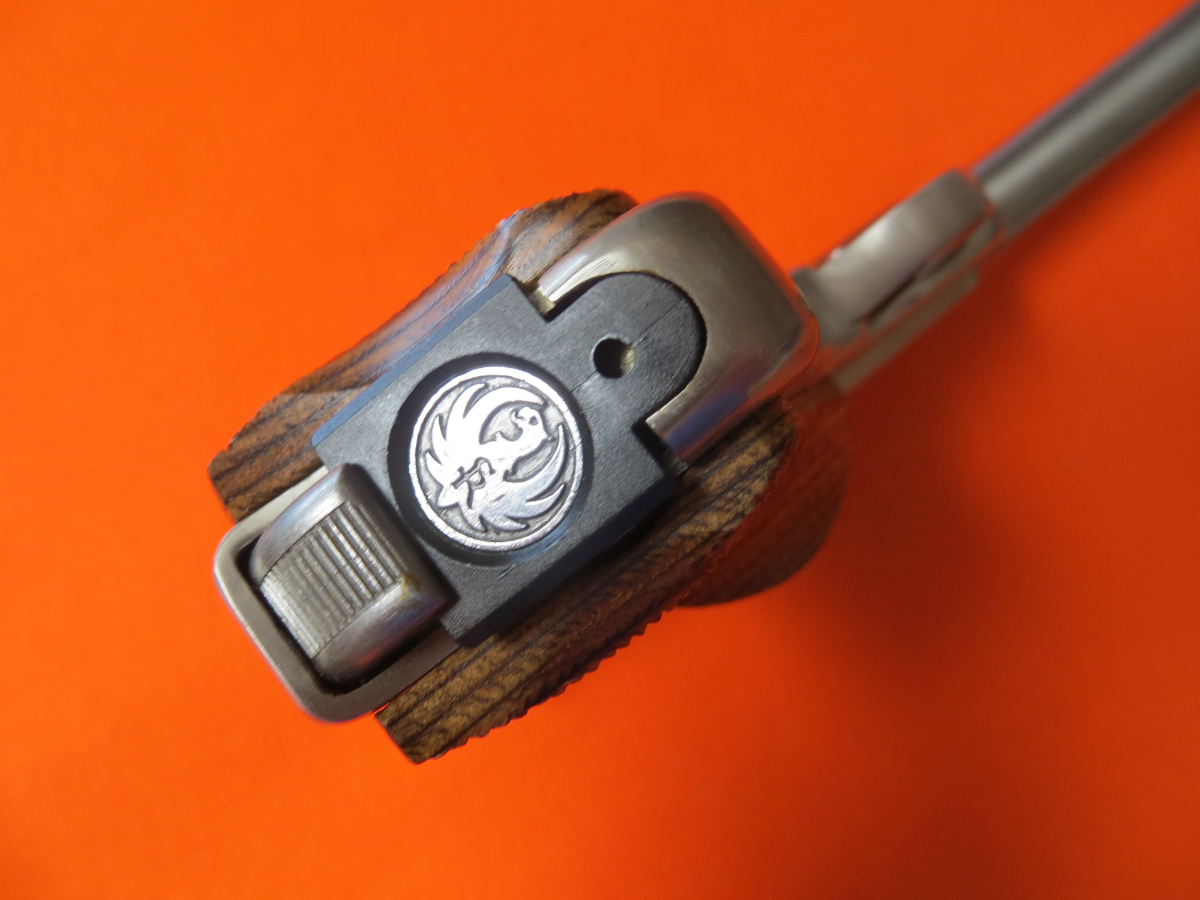
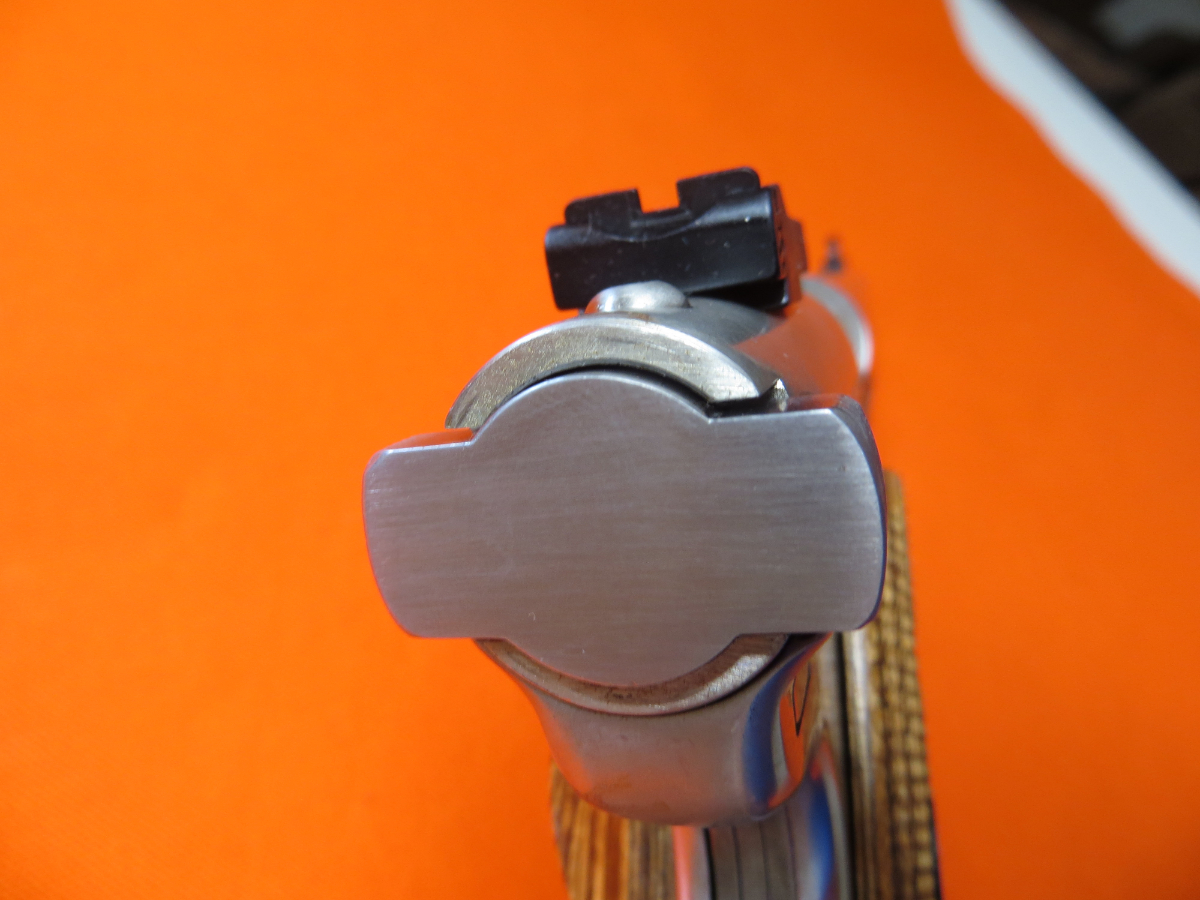
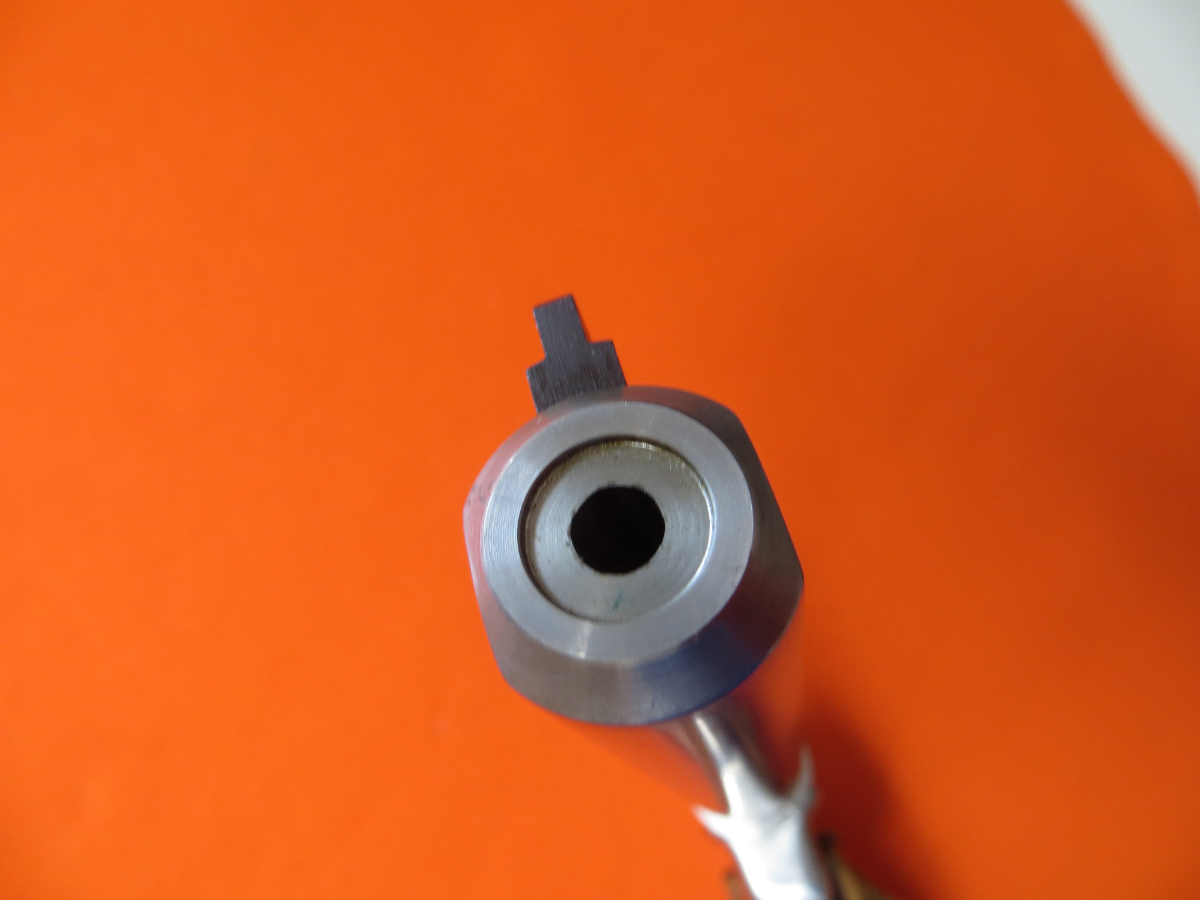
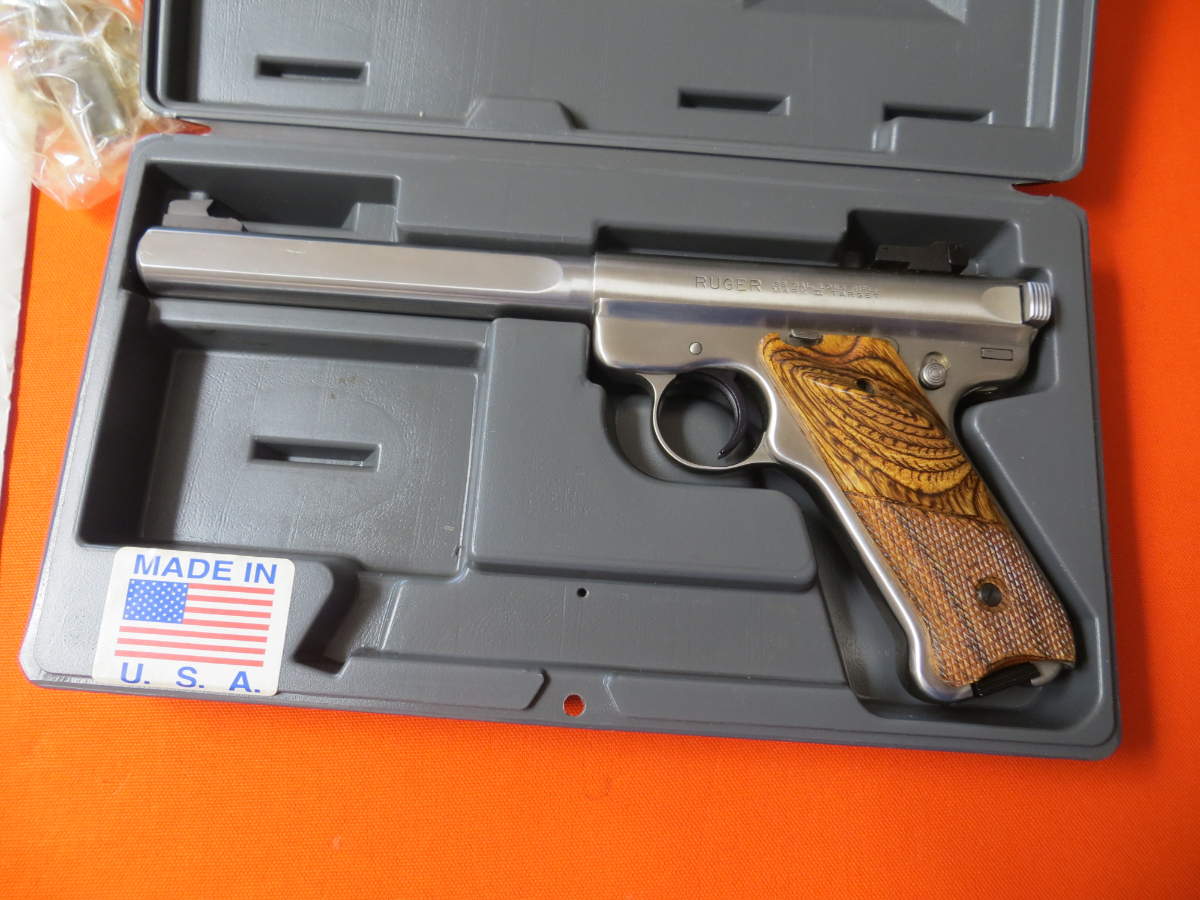
All percentages in this essay are in terms of the total charge weight.
In almost any reference or official document, propellant weight is given as a fixed number. In reality, as each batch or lot of propellant will be slightly different in its energetic power from any other lot, the weight of an individual charge will depend upon just how “powerful” was the lot of propellant from which it was made. In order to ensure consistency in muzzle velocity from shot to shot, a “Charge Assessment” is made for each lot to determine the proper weight for individual charges. This means that the actual weight of a charge from a particular batch of propellant may be different than a charge made from a different batch of propellant. This is especially the case for large-caliber guns which use a very heavy charge. So, when you see a charge weight given for any particular weapon, understand that this is really the nominal weight of the propellant charges and may not the the actual weight of all charges for that weapon.
In 1892, the Austro-Hungarian Imperial Navy started using a single-based “smokeless powder” designated as M.92 consisting of 100% nitrocellulose (12.3% nitrogen). There appears to have been three variations of M.92 manufactured, with slight differences between the different types. Like other pure nitrocellulose propellants of this time, the M.92 types were unstable and in 1893 the Navy switched to a double-based nitrocellulose/nitroglycerin propellant designated as M.93. This had no stabilizer elements and again proved unstable.
In 1897 the Navy introduced a new double-based propellant designated as M.97 that included barium nitrate as an oxidizer and vaseline as a stabilizer. This proved more stable than the earlier propellants and became the basis for all subsequent propellants in use until the end of World War I and the dissolution of the Austo-Hungarian Empire. Over the next two decades, the percentages of ingredients of this propellant were changed several times but all were known as M.97 with a letter suffix indicating the change.
The table below shows the composition of these propellants – percentages given in official documents do not always add up to 100%.
Designation | Nitrocellulose % (Nitrogen %) | Nitroglycerin % | Barium Nitrate % | Vaseline % |
---|---|---|---|---|
M.92 | 100.0 (12.0 to 12.1) | -0.0- | -0.0- | -0.0- |
M.92a | 100.0 (12.8) | -0.0- | -0.0- | -0.0- |
M.92b | 100.0 (12.2 to 12.35) | -0.0- | -0.0- | -0.0- |
M.93 | N/A | N/A | -0.0- | -0.0- |
M.97 | 52.0 (12.0 to 13.3) | 37.0 | 8.25 | 2.0 |
M.97a | 52.0 (12.0 to 13.3) | 33.0 | 8.5 | 4.0 – 5.0 |
M.97b | 52.0 (13.3) | 37.0 | 8.25 | 2.0 |
M.97c | 41.0 (12.3) | 41.0 | 16.5 | 1.5 |
M.97d | N/A | N/A | N/A | N/A |
M.97e | N/A | N/A | N/A | N/A |
M.97f | 62.0 (12.6) | 25.0 | 8.0 | 3.0 |
M.97h | N/A | N/A | N/A | N/A |
M.93, M.97d, M.97e and M.97h were produced prior to 1914 but we have been unable to find details on their composition.
The chemical composition of the M/97a propellant manufactured in Blumau differed slightly from the one made by the Dynamit Nobel Pozsony (Bratislava). The nitroglycerin content of the Blumau powder was a little higher than that of the Pozsony powder.
The use of barium nitrate in the M.97 series gave their muzzle flashes a greenish tint.
Almost all propellants were manufactured in the form of hollow tubes (Rohrenpulver). Rohrenpulver was used in most guns 12 cm and larger but at least in the early 1900s 15 cm guns used propellants in strip form (Bandpulver).
Cordite was widely used by the British with Mark I being the first version produced, with manufacturing starting in 1889. This propellant was much more powerful and thermally efficient than gunpowder or brown powder, as shown by tests with early British 6 inch (15.2 cm) QF guns. These guns replaced their 55 lbs. (25 kg) charge of brown prismatic powder with only 13 lbs. (6 kg) of the new Mark I cordite propellant. Mark I cordite consisted of 37% nitrocellulose (13.1% Nitrogen), 58% ntroglycerin and 5% petroleum jelly. This last ingredient had originally been used as a lubricant during the manufacturing process, but it was found that it also acted as a stabilizer as its unsaturated hydrocarbons counteracted the byproducts of the decomposition process.
As can be easily guessed by the name, Cordite was primarily manufactured in thin cylindrical or cord form, with the different sizes denoted by a number representing the hole diameter of the extrusion die. For Mark I cordite, these numbers were in 0.010 inch (0.254 mm) increments. For example, Cordite 30 meant Cordite Mark I extruded through a die having holes 0.300 inches (7.62 mm) in diameter. It should be noted that using propellant in cord form means that the burning surface decreases as the propellant burns and that with hindsight it would have been better to adopt a tubular form, as was done in Germany. Tubular forms have a constant burning surface and thus produce more gas to fill the expanding volume as the projectile travels up the barrel.
Cordite Mark I was first issued for 3-pdr, 6-pdr, 4.7-inch and 6-inch guns in 1893 and for 12-inch guns in May 1895. Generally, the larger the gun, the larger the cord sized used. For example, the 12″ (30.5 cm) Mark VIII and IX guns used Cordite 50, the 6″ (15.2 cm) guns used Cordite 30 and the Hotchkiss 3-pdr guns used Cordite 5.
Mark I cordite did burn very hotly and this was found to be detrimental to gun barrel life, as the high temperatures caused rapid wear. For this reason, the proportions of ntroglycerin and nitrocellulose were revised in order to increase the barrel life. This new propellant was designated MD (for Modified) and it came into service in 1901. MD cordite consisted of 65% nitrocellulose (13.1% N), 30% ntroglycerin and 5% petroleum jelly. MD charges were about 25% heavier than Mark I for the same ballistic result but doubled the life of the guns. MD did have a high shrinkage rate during the drying process, with cords that were extruded at 0.45 inches (1.14 cm) in diameter shrinking down to as little as 0.34 inches (0.86 cm) after they dried. A tube form was made for at least the 4-inch (10.2 cm) QF Mark III, but most guns still used the cord form. Like Mark I cordite, the different sizes of MD were denoted by a number representing the hole diameter of the extrusion die and the numbers were in 0.010 inch (0.254 mm) increments. The most common sizes were MD4.5, which was used for 3-pdr guns, MD8, MD11, MD19, MD26, MD37, which was used for 9.2-inch (23.4 cm) guns and MD45 which was used for the 12-inch (30.5 cm) and larger guns. A larger diameter MD55 cord was tried as this would have been advantageous for the larger caliber guns, but it was found to be impossible to remove all of the volatile solvent.
Both Mark I and MD were in use during World War I, and both had poor storage characteristics with their stability degrading over time. A study performed after World War I found that MD tended to form highly unstable micro-sized dust particles consisting of nitrocellulose and iron pyrites. These unfortunate traits led to several ships suffering magazine explosions during World War I, both in action and in harbor.
By April 1917 considerable improvements had been made in the manufacture of cordite by changing to the use of clean carded sliver cotton, substituting cracked mineral jelly for petroleum jelly, using guncotton which had been nitrated for a minimum of 2.5 hours and in using inspectors for quality control at all stages of the process. This improved propellant was known as MC (for Modified Cracked) and the substitution of cracked mineral jelly in place of petroleum jelly was in a bid to improve stability. With this exception, MC cordite was chemically similar to MD cordite. Plans were put in place during the spring of 1917 to replace some 6,000 tons (6,100 mt) of old cordite with MC cordite as soon as production permitted. However, after the battleship Vanguard exploded in harbor in July 1917, this program was expedited and the exchange was completed in ships of the Grand Fleet by March 1918 and in all ships by September 1918. MC cordite was a fairly satisfactory propellant if properly and carefully made and it was still in use during World War II, primarily as an alternative propellant for certain guns.
In 1927, following a study of the German RP C/12 solventless propellant (see below) used during World War I, British chemists developed a more stable version of cordite called SC (solventless cordite, also known as solventless carbamite). This was used to replace the older propellants as rapidly as possible and remained in service until well after World War II. SC was primarily manufactured in cords (strings) but some was also made in tubular form. The nomenclature was changed such that the cord die hole diameter was now given in 0.001 inch (0.0254 mm) increments. SC consisted of 49.5% nitrocellulose (12.2% N), 41.5% ntroglycerin and 9% centralite (also known as “carbamite”), which was used as a stabilizer. Centralite not only improved the stabilization of SC cordite, it did not have to be removed during the manufacturing process, which gave it better dimensional stability as well. This also permitted the use of larger diameter cords, with the largest being SC500 which was used for the 14-inch Mark VII guns at Dover for cross-channel firings. However, SC was a stiff material to extrude and needed much higher pressures than did the Cordite MD type.
A hotter burning propellant known as HSC (for Hot Solventless Carbamite) or HSCT (for Hot Solventless Carbamite Tubular) for 6-pdr, 3-pdr and 2-pdr guns was also produced. This was composed of 49.5% nitrocellulose, 47% ntroglycerin and 3.5% centralite.
SC was used extensively during World War II and had a better safety record than the previous cordites, although the loss of HMS Hood may be partially attributed to it.
Nitrocellulose propellant imported from USA sources in flake or tube form was standard for Oerlikon 20 mm guns during World War II. In addition, the USA DuPont chemical company NH and FNHP propellants of nitrocellulose dinitrotoluene type in multi-tube form were extensively used for guns between 4 inch (10.2 cm) and 5.25 inch (13.3 cm). The short multi-tube grains of these propellants were particularly well-suited for bottle-neck cases such as those used for the 4.5 inch (11.4 cm) guns. NH was composed of 86% nitrocellulose (13.15% N), 10% dinitrotoluene, 3% dibutylphthalate, 1% diphenylamine while FNHP differed in having 2% less nitrocellulose and 2% more dibutyl phthalate with 0.8% potassium sulfate. FNHP was commonly used for Bofors 40 mm cartridges.
Due to the presence of calcium in the small amount of chalk used to counteract traces of residual acids, SC cordite had a very bright “flash,” a characteristic which led to the development of flashless propellants. British flashless propellants in use during World War II were produced in primarily in slotted tubular form. The most used was NF, originally known as NFQ, and this was composed of 55% picrite (nitroguanidine), 16.5% nitrocellulose (12.1% N), 21% ntroglycerin, 7.5% centralite and 0.3% cryolite. NF was not easy to make and the basic initial material required for picrite was calcium carbide, which required large amounts of electricity during the manufacturing process. For this reason, the only plant making this propellant was located at Welland near Niagara Falls in Canada. Canada also produced Cordite N during World War II which was widely used as a propellant for aircraft gun ammunition. Cordite N is another triple-base propellant that was very cool burning and produced little smoke and almost no flash. The composition was 55.0% nitroguanidine, 19.0% nitrocellulose, 18.5% nitroglycerin and 7.5% ethyl centralite. Cordite N does not appear to have been used as a naval gun propellant in the Royal Navy, but a variation of it was used by the USN (see below).
Flashless propellant was in great demand during the war, however, for guns larger than 5.25″ (13.3 cm), full flashless charges became too bulky for existing turret arrangements and so the only larger weapon issued these was the 6″ (15.2 cm) Mark XXIII. These were actually “reduced flash” or “non-blinding” charges and were designated as NQFP. This propellant was issued in cord form and differed from NF by having 4.5% more nitrocellulose, 4.5% less centralite and 2% potassium sulfate.
The 114 mm (4.5″) Mark 8 naval gun uses a triple-base (Nitroguanidine, Nitroglycerin and Nitrocellulose) flashless propellant known as MNLF/2P/M08. This is manufactured in tube form.
Notable among British double-base propellants was CSP2 (for Chilworth Special Powder No. 2) made by the Chilworth Gunpowder Company prior to World War I. This propellant was widely used by the armament firm of Elswick for many of their export weapons as an alternative to cordite. CSP2 consisted of 70.5% nitrocellulose, 23.5% ntroglycerin, 5% petroleum jelly and 1% sodium bicarbonate. After 1910, this propellant was also manufactured by the Nobel Dynamite Company of Avigliana, Italy.
As noted above, British cordite propellants were designated by the type and a number representing the hole diameter of the extrusion die. For Mark I, MD and MC formulations, these numbers were in 0.010 inch (0.254 mm) increments and for SC cordite they were in 0.001 inch (0.0254 mm) increments. For example, MD45 meant MD-type cordite manufactured with dies having 0.450 inch (11.4 mm) diameter holes while SC350 meant SC-type cordite manufactured with dies having 0.350 inch (8.89 mm) diameter holes.
Propellant grains made in the form of tubes were designated by the type of propellant followed by two numbers, with the first number indicating the external diameter and the second the internal diameter, both in 0.001 inch (0.0254 mm) increments. SC in tubular form was designated in the form of SC T 100-40. HSC and HSCT designations were in the form of HSCT/K 134-055 with the K indicating that potassium cryolite was used as a moderator. NF designations were of the form NF 164-048.
The first “smokeless powder” propellant was invented by the French chemist Paul Vielle in 1884 and adopted by the Navy around 1890. Known as Poudre B (for poudre Blanche, meaning “white powder” and also known as poudre Boulanger marine after the Minister of War, General Georges-Ernest Boulanger), this was a single-base propellant composed primarily of nitrocellulose. This early French nitrocellulose was susceptible to spontaneous ignition, and is believed have caused the loss of the battleships Liberté and Iéna, but this propellant was improved by the addition of diphenylamine as a stabilizer and by more careful attention to the pulping and cleaning process to remove residual traces of acid. The French continued to use single-base nitrocellulose in a strip form for most of their weapons up to World War II. These propellants were designated as BM (for Blanche Modifié? – Modified White?) followed by a number which indicated thickness, such as BM15. This number was somewhat arbitrary, but a larger number did indicate a thicker strip. During the war, BM was produced in a reduced flash version using potassium chloride for some 138.6 mm guns.
French “solventless” propellant designated as SD was produced during the 1930s for a few guns including the 380 mm and 330 mm. Like British SC, French SD appears to have been developed from a study of German RP C/12, as it was in the form of a single tube grain and the composition was similar in its proportions of nitrocellulose, nitroglycerin and centralite. The actual composition of SD was 64-65% nitrocellulose, 25% nitroglycerin and 8-9% centralite. Like BM, the SD designation was followed by an arbitrary number with a larger number indicating a larger grain size. SD19 was issued for 330 mm guns while SD21 was issued for 380 mm guns. The grain for SD19 was 14 mm (0.55 in) outside diameter and 4 mm (0.157 in) internal diameter. The grain for SD21 was a larger tube, but the dimensions are unavailable at this time.
German propellants for the first half of the twentieth century were manufactured in the form of hollow tubes and designated as RP for Rohr-Pulver or “Tube powder.” The propellants were classified by model year and by the external and internal diameters of the tubes in millimeters. For example, RP C/38 (14/4.9) meant a tube powder first introduced in 1938 that had an external diameter of 14 mm (0.551 in) and an internal diameter of 4.9 mm (0.193 in).
Prior to 1912, the Germans used solvents in their manufacturing process, including for RP C/06, the standard propellant in use prior to World War I. There were several compositions used between 1912 and 1945, all of a solventless double-based nature using centralite (symmetrical Diethyl Diphenyl Urea) as a non-volatile solvent. Centralite was not removed from the finished propellant and acted as an excellent stabilizer. Leaving this solvent in also greatly reduced shrinkage during the drying process.
The first of these solventless propellants, RP C/12, was the primary propellant used during World War I. This and RP C/32 used nitroglycerin while formulations starting with RP C/38 used diethylene glycol dinitrate (DGN), which was cooler-burning and less bore erosive.
All of these formulations were resistant to exploding even when exposed to a hot fire. For instance, when the small battleship Gneisenau was bombed at Kiel in 1942, over 23 tons (24 mt) of RP C/32 propellant was ignited in a forward magazine. There was no explosion even though the 750 mt (738 ton) turret “Anton” was lifted at least 50 cm (20 inches) from its mounting by the gas pressure generated by the deflagration. As noted above, both the British and the French did extensive studies of RP C/12 after World War I and developed their own “solventless” propellants based upon the results.
Propellant | Chemical | |||||||||
---|---|---|---|---|---|---|---|---|---|---|
Nitrocellulose | ntroglycerin | DGN | Petroleum jelly | Sodium bicarbonate | Centralite | Akardite | Methyl centralite | Magnesium oxide | Graphite | |
RP C/06 | 70.5% (about 12% N) | 23.5% | – | 5% | 1% | – | – | – | – | – |
RP C/12 | 64.13% (11.9% N) | 29.77% | – | – | – | 5.75% | – | – | 0.25% | 0.10% |
RP C/32 | 66.6% (11.5% N) | 25.9% | – | – | – | 7.25% | – | – | 0.15% | 0.10% |
RP C/38 | 69.45% (12.2% N) | – | 25.3% | – | – | 5.0% | – | – | 0.15% | 0.10% |
RP C/38N | 68.72% (12.2% N) | – | 25.03% | – | – | 1.5% | – | 4.5% | 0.15% | 0.10% |
RP C/40 | 67.55% (11.45% N) | – | 24.6% | – | – | 7.5% | – | – | 0.25% | 0.10% |
RP C/40N | 64.87% (12.2% N) | – | 23.63% | – | – | – | 0.5% | 7.0% | 0.15% | 0.10% |
Many references have conflicting information on propellant weights for the World War II period. As can be seen above, part of this confusion lies in that the Germans used several different formulations during this time and also used different grain sizes in making up charges for the same gun. German official documents for these guns in describing the propellant charges often used the term “zu etwa – “to about” – to indicate that the actual charge weight stenciled on a cartridge might not match the weight given in the document.
Italian propellants before World War II were designated as C and were typically a mixture of 68.5% nitrocellulose, 25.5% ntroglycerin, 5% petroleum jelly and 1% sodium bicarbonate. This propellant was apparently derived from Elswick CSP2 and was chemically similar to the German RP C/06. In 1936 solventless propellants were introduced with NAC from Dinamite Nobel and FC4 from Bombrini-Delfino. NAC contained 66% nitroacetylcellulose (this was nitrocellulose mixed with a small amount of acetyl cellulose), 27% ntroglycerin and 7% centralite. FC4 was 64% nitrocellulose, 28% ntroglycerin, 4% phthalit, 3% centralite and 1% petroleum jelly. Grains were usually of single tube design, although the charges for the 381 mm/50 (15 inch) guns also had a disk propellant at the igniter end, possibly to speed up the charge ignition. Reduced flash propellants were introduced during the war by the addition of potassium chloride with charges being produced for gun calibers between 12 cm (4.7 inches) and 20.3 cm (8 inches).
Postwar, the Italians have adopted a singe-based propellant similar to the USN’s NACO (see below). These are designated with M numbers, such as M8 or M10.
Before 1893 the Japanese Navy used brown prismatic powder which was purchased from Britain, Holland or Belgium. In 1888, the Japanese Army, which was responsible for procuring propellants both for itself and for the Japanese Navy, tested the French Poudre B propellant. The tests results were acceptable, and the Japanese purchased a production plant in 1893.
British Mark I Cordite was introduced to Japan the same year when the British-built cruiser Yoshino entered service. On 19 March 1903, Cordite Mark I, which the Japanese designated as C and called Jinjô Chûjô (“common cord like powder”), was adopted for all QF-type guns then in service with the Navy.
Until after the Russo-Japanese War, all naval propellants were imported but in 1907 the Japanese let a contract to the Sir William Armstrong Co. to build a factory at Hiratsuka City, Kanagawa Prefecture, for the manufacture of British MD cordite. The plant was completed in December 1908 and produced both MDC cords and MDT tubular propellant. In 1919, the Japanese Navy purchased this factory outright and renamed it the Kaigun Kayakukô (Naval Powder Plant).
In 1912, the Japanese developed and produced their first naval propellant, known as C2 for Type 2 Cordite. Officially adopted on 12 September 1917, this consisted of 65% nitrocellulose, 30% ntroglycerin, 3% mineral jelly and 2% jara jara (beta naphthol methyl ether). This propellant was also made in a tubular form (tubite) and in this form was known as T2. In 1920, centralite was introduced as a gelatinizer, a technique used by the Germans in their RP C/12. By 1924, this had become the standard naval service propellant and was known as DC (for Doku = Deutsch or German Cordite).
Fairly satisfactory flashless propellant containing potassium sulfate and hydrocellulose was introduced about 1938. Known as FD, this was said to reliably eliminate flash for guns up to 14 cm (5.5 inch) but not for larger guns.
The nominal diameter of the Japanese cords was given in units of 0.1 mm (0.004″). For example, the Japanese propellant 80DC was cordite with cords of 8.0 mm (0.315″) diameter.
By 1896 the USN had begun small-scale production of a single-base nitrocellulose propellant at Newport, Rhode Island. Major manufacturing of this “smokeless powder” SP at the Naval Ordnance Station (later known as the Naval Powder Factory), at Indian Head, Maryland was begun in 1900 and continued there for decades.
Smokeless powder will deteriorate over time as it contains nitrocellulose and two volatile substances, ether and alcohol. Its length of usefulness depends largely on the conditions under which it is stowed. Moisture or heat speeds its deterioration and the combination of the two is extremely damaging to the propellant. In 1905, George Patterson, the key civilian researcher at Indian Head, was experimenting with the addition of rosaniline dye to the propellant, designating these lots as SPR. This dye did nothing to stabilize the deterioration of the propellant, but instead showed the status of the deterioration by changing color as it combined with the forming acids.
Patterson recommended the abandonment of rosaniline dye in 1908 in favor of adding diphenylamine as a stabilizer. Known as SPD, this new propellant was first produced in 1908 and adopted as the standard propellant formulation by 1912. SPD was found to have good stability characteristics when properly stored, with some lots manufactured prior to World War I staying in storage for as long as twelve years without loss of stability. During World War II, the primary USN propellant was SPD in a multi-tube form made up of 99.5% nitrocellulose (12.6% N), 0.5% diphenylamine. The USN used a flat, short cylindrical grain design that usually had seven perforations with the websize varying from 0.023 in (0.58 mm) for the short 3 in (7.62 cm) gun to about 0.174 in (4.42 mm) for the 16 in (40.64 cm) guns. SPD had a good safety record partly due to the harder-to-ignite and slow burning nature of its single-base nature and partly due to the quality of its manufacturing process.
In the mid-1920’s, both the Naval Powder Factory at Indian Head and the DuPont Co. developed flashless powders. The Powder Factory had also obtained good results by mixing flash-reducing chemicals with the conventional powder charge. Flashlessness, however, was gained only by an increase in the amount of smoke, which was unacceptable to the fleet as it interfered with searchlight illumination and fire control. By 1928, BuOrd had stopped work on flash suppression. With the advent of radar in World War II, smoke became less objectionable and the fleet was willing to accept considerably more smoke in order to obtain a significant reduction in flash. At the time the request for flashless powder was received, BuOrd had already accumulated large inventories of smokeless powder. In order to prevent this material from being discarded, some means of converting it into acceptable flashless charges had to be found.
By the summer of 1942, the Naval Powder Factory had the answer in a chemical tablet made of a mixture of potassium nitrate and potassium sulfate, to which was added a small amount of graphite to facilitate pelleting. After extensive testing by the Naval Proving Ground had worked out the details, production was begun in September 1942. The use of these flashless pellets was limited to guns between 3 to 6 inches (7.62 to 15.2 cm) as larger calibers would have required too many pellets. Even in these calibers performance was not always perfect. A fused mass of clinkers could form in the gun chambers, a result of incomplete combustion of the pellets. At high angles of gun elevation, these clinkers could cause gun casualties such as jammed breech mechanisms. To eliminate the hazard, the Research Division of BuOrd, working with the Naval Powder Factory, developed a flashless grain. Known as SPDF, this new material consisted of 5 to 7 percent potassium sulfate mixed with nitrocellulose, colloided as a normal smokeless powder, and extruded in the form of a powder grain. Satisfactory in both ballistic and flash suppression properties, flashless grains of this type were in production at the Naval Powder Factory when the war ended. Meanwhile, pellets continued to serve the need for a flash suppressor for existing propellants. While not completely satisfactory, these two compositions provided the fleet with an essentially flashless charge long before it was possible to have true flashless powder.
During World War II some Cordite N (see above) flashless propellant was imported from Canada and this was used for full charges for at least 6 inch (15.2 cm) and 8 inch (20.3 cm) guns and in reduced charges for 16 inch (40.6 cm) guns during the war and for other guns afterwards. Known as SPCG in USN service, the composition of this propellant differed from British NF and consisted of 19.0% nitrocellulose (13.1% N), 18.7% ntroglycerin, 55% nitroguanidine and 7.3% centralite. BuOrd was unhappy with this propellant, as Cordite N was brittle and, even worse, it contained ntroglycerin, which the USN considered to be highly undesirable for use in naval propellants. BuOrd instituted a major research program to develop a flashless propellant that did not use ntroglycerin. After testing dozens of possibilities, scientists narrowed the field to two likely candidates – dinitrodiethanol nitramine (DINA) and Fivonite. Experimental firing at Dahlgren showed little difference between the two, but DINA was selected because of its superior physical properties.
Albanite, the name given this new flashless powder because of its white color, appeared to have all the desirable features of Cordite N and few of the objectionable ones. Studies of Albanite by DuPont demonstrated the feasibility of large-scale production, and by V-J Day BuOrd had launched an ambitious procurement program which called for monthly deliveries of 4,000,000 pounds of the new propellant. Albanite was composed of 20.0% nitrocellulose (12.6% N), 19.5% DINA, 55.0% nitroguanidine, 4.0% dibutyl phthalate and 1.5% centralite. To this mixture was added a small amount of potassium sulfate and lead which acted as a decoppering agent. These charges weighed about 10% more than those for nitrocellulose.
In the early 1950s experiments with a solventless propellant known as NOSOL progressed into the current formulations of single-base propellant known as “Navy Cool” or NACO which is composed of 91% nitrocellulose (12.0% N), 1% ethyl centralite, 3% butyl stearate, 1% basic lead carbonate, 1% potassium sulfate and 3% volatiles.
The cancelled ERGM rocket projectile was to use a special mixture known as EX-99 propellant which, according to one open-source document, is composed of 76% RDX (cyclonite, cyclomethylene trinitramine), 12% cellulose acetate butyrate (CAB), 7.6% acetal/formal (A/F), 4% nitrocellulose and 0.4% ethyl centralite. The high percentage of RDX gives this propellant the unusually high “kick” necessary for this relatively heavy projectile and is one of the reasons why the 5″/62 (12.7 cm) gunhouse was greatly strengthened over the earlier 5″/54 (12.7 cm) gunhouse.
The designations below are normally followed by a number that indicates the sequence of manufacture. The combination of the letters and the number is termed the index or the lot of the powder.
SP – Smokeless Powder, the original single-based propellant adopted by the USN around 1896
SPR – Smokeless Powder with Rosaniline dye, in service with the USN for a brief period between 1905 and 1908
SPD – Smokeless Powder with Diphenylamine as a stabilizer, adopted by the USN in 1908
SPDB – A blend of diphenylamine stabilized powders of different lots. The purpose of blending is to provide a uniform index of ample size and desired characteristics from smaller remnant lots.
SPDF – A flashless formulation of SPD
SPDN – SPD with nonvolatile materials added to reduce its hydroscopic tendencies. The N stands for nonhygroscopic.
SPDW – Reworked propellant intended for target use. Propellant is ground down, reprocessed and then made into new grains.
SPWF – Reworked propellant to which a flashless element has been added
SPDX – Water-dried SPD
SPC – Smokeless Powder with Carbamite (ethyl centrality) added for stability
SPCF – A flashless formulation of SPC
SPCG – Flashless triple-based propellant stabilized with carbamite. The G is short for NG, the designation for Nitroguanidine.
Campbell, John
– Jutland: An Analysis of the Fighting. Conway Maritime Press, Ltd., 1986
– Naval Weapons of World War Two. Conway Maritime Press, Ltd., 1985
– Technical Topics No. 5: Cordite. Article published in Warship Volume II, Conway Maritime Press, Ltd., 1978
Carlisle, Rodney. Powder and Propellants: Energetic Materials at Indian Head, Maryland, 1890-2001 (Second Edition). University of North Texas Press, 2002
Gander, Terry J. and Charles Q. Cutsaw. Jane’s Ammunition Handbook, Ninth Edition 2000-2001. Jane’s Information Group, Inc., 2000
Garzke, William H. Jr. and Robert O. Dulin, Jr. Battleships: United States Battleships, 1935-1992 (Revised and Updated Edition). Naval Institute Press, 1995
Green, Constance McLaughlin, Harry C. Thomson and Peter C. Roots. The Ordnance Department: Planning Munitions for War. Office of the Chief of Military History, Department of the Army, Washington, D.C., 1955
Johnson, Ashley. “Closed Loop Energetics with VOC Emission Reduction (CLEVER).” ESTCP Cost and Performance Report. Environmental Security Technology Certification Program (ESTCP), Department of Defense (DoD), June 2003
Krámli, Mihály – Supplied official documents from the Austrian and Hungarian archives
Lacroix, Eric and Linton Wells III. Japanese Cruisers of the Pacific War. Naval Institute Press, 1997
Mosher, Paul. US Patent No. 4082583, “Solventless double base propellants and method for plasticizing MTN nitrocellulose propellants without use of solvents.” U.S. Department of Patents, issued 4 April 1978
Tauzla, Jean-Michel. An Introduction to Energetic Materials. SNPE Matériaux Energétiques, 2005
US Navy, Bureau of Ordnance (BuOrd). O.P. 1664 Volume 1 – U.S. Explosive Ordnance, 28 May 1947
US Navy. “Report O-10-2: Japanese Propellants – Article 2, Rocket and Gun Propellants – General.” Reports of the U.S. Naval Technical Mission to Japan, 29 November 1945
16 February 2008 – Benchmark
10 January 2009 – Additional information on British cordite propellants
28 February 2018 – Updated to HTML 5 format
02 October 2020 – Added Austria-Hungary propellant section
01 April 2021 – Added details to French section
26 March 2022 – Added explanation for “zu etwa” for German propellants, minor changes to ERGM propellant not
On the left side of the receiver, you’ll find one large threaded hole and two smaller ones fitted with screws. These permit installation of a receiver sight. At one time Lyman made a sight specifically for the 1895; today you can get a reproduction of the sight from Buffalo Arms. Just be mindful that when shopping for sights you’ll see references to 1895 that refer to Marlin and not Winchester.
Williams still makes a receiver sight for the Winchester 1895, but the company notes its FP-Winchester 71 will not fit on .405 Win. versions of the rifle.
I love the wood on this gun. It’s oil-finished black walnut, nothing fancy but with a handsome grain. The checkering is done in a bordered point pattern, and it’s very nicely executed. The well-shaped fore-end feels good in the hands and features a graceful Schnabel tip. Wood-to-metal fit is proud all the way around, but at least it’s consistent. As befits a lever action of its era, there are no sling swivel studs.
The buttstock has a plain, black metal buttplate. It’s traditional, if not particularly comfortable to shoot.
While the current rifle is also available in .30-06, I think for most people the .405 Win., which made its debut in 1904, will be the more interesting chambering. It’s a straight wall with a case length of 2.583 inches, longer than both the .444 Marlin (2.225 inches) and .45-70 Gov’t (2.105 inches).
Hornady’s current load throws a 300-grain pointed softpoint bullet at 2,200 fps out of this rifle, and for once the chronograph figures I got exactly matched the book specs. That translates to 3,225 ft.-lbs. of energy at the muzzle.
To put this in context, it’s considerably more energy than most 300-grain .45-70 loads (around 2,200 ft.-lbs.), although, of course, factory loads for the Government are purposely held low because of all the old rifles out there. The .405 also outdoes Hornady’s 265-grain LeverEvolution load in the .444 Marlin at 3,180 ft.-lbs., but the .444 Marlin Superformance (3,389 ft.-lbs.) and LeverEvolution .450 Marlin (3,572 ft.-lbs.) are more powerful.
Roosevelt felt the .405 was a fine lion cartridge, but he and his son Kermit also used it to take rhinos and even elephants. Results on the latter were decidedly mixed, and Roosevelt admitted it was a bit wanting at the largest end of the game spectrum.
“Our experience had convinced us that both the Winchester .405 and the Springfield .300 [.30-06] would do good work with elephants; although I kept to my belief that, for such very heavy game, my Holland .500/450 was an even better weapon,” he wrote in African Game Trails.
As an aside, I was discussing this cartridge with Craig Boddington, and he told me his daughter Brittany used the .405 Win. on Cape buffalo. However, she was shooting the cartridge in the stronger Ruger No. 1 action, which allows the round to be loaded much hotter and with heavier bullets than would be safe even in a modern-built 1895.
So if this cartridge has acquitted itself well in the hunting fields, why is it so obscure? Part of the reason is its oddball .411 bullet diameter. It’s close to the .410 diameter of the .450/400 Nitro Express 3-inch, which is justifiably admired as a dangerous-game cartridge, but the Nitro pushes a 400-grain bullet at 2,050 fps for 3,700 ft.-lbs. of energy.
From there, you’ve got the various powerful .416s, which use .416-inch bullets as their designation suggests. And then there’s the .404 Jeffery, a superb dangerous-game round. Ironically, while .405 is a bigger number than .404, the Jeffery takes a .423-inch bullet.
Bullet size notwithstanding, even in the .405’s heyday the majority of big game hunting in the United States involved deer-size game, and while today you would include hogs as well, then as now there isn’t a ton of call for a cartridge on the .405’s power level.
But speaking of wild boar, Boddington said with the standard 300-grain load it’s “lights out” on hogs, and it certainly has enough energy to tackle the biggest North American game. And today we’re seeing a resurgence in straight-wall cartridges due to some formerly shotgun-only states now allowing straight-wall centerfires for deer hunting. Could the .405 fit in here?
If you zero at 100 yards, the .405 is dropping 8.3 inches at 200 yards and 30.2 inches at 300 yards—with 1,727 ft.-lbs. and 1,250 ft.-lbs. of energy respectively. While that’s a lot of energy, it doesn’t stack up as well in terms of trajectory. Cartridges like the .350 Legend, .450 Marlin, .444 Marlin and .450 Bushmaster are dropping in the 4.5- to 5.7-inch range at 200 yards, with the .45-70 close to seven inches.
But trajectory is just a number. If you range-confirm your drop and do the math, you can still hit your target—and with the .405 you can be sure you’ll be delivering sufficient power.
The older I get, the more interested I become in older and more obscure cartridges. The .405 Win. certainly qualifies, and I think the 1895 would be a fantastic wild boar, elk, bear or moose hunting companion, and it would be a unique deer rifle as well.
I grant you it’s not a ton of fun from the bench. The straight stock with its 27/8-inch drop and hard metal buttplate accentuate recoil forces, but it’s way more pleasurable to shoot than a big, high-pressure magnum.
I did manage to generate some good groups from the bench with the iron sights, albeit at 50 yards. One hundred yards ain’t happening with my eyes and sights like these, at least not for a realistic assessment of the rifle’s accuracy potential. However, I found that by placing the gold bead of the front sight so it sat just atop the fine portion of the notch, I could get an okay sight picture.
While the .405 is distinctly lacking in factory offerings, fortunately for the 1895 it loves Hornady’s 300-grain load. The average wasn’t bad, and I was able to shoot one group under an inch, all shots touching—indicating that with younger eyes and/or an aperture sight you could get plenty of accuracy. I did shoot a couple 100-yard groups just for fun, and they came in around 2.5 inches—generally in line with what I got at 50 yards.
I worked up four handloads with Hodgdon H4198 and the same Hornady bullets found in its factory ammo. I began with the starting load listed in the Hodgdon manual and ended one grain short of max. The rifle didn’t like the starting load at all, and it’s not included in the accompanying accuracy chart. It’s interesting to see how the accuracy improved as velocity went up, so this gun seems to like ’em on the warm side.
Shooting from field positions was fun. The lever works smoothly, and the rifle comes back on target reasonably quickly thanks to its eight-pound weight—which isn’t a bad field-carrying load at all. At 50 yards offhand I could keep all of my shots in a volleyball with a relatively rapid rate of fire. I also shot the rifle from unsupported sitting at 100 yards and would have all the confidence in the world I could hit a six-inch vital zone every time.
Cartridges load easily into the straight-stack internal magazine, snapping home with a satisfying “snick.” Feeding was flawless.
I always find it enjoyable to work with a rifle that has a storied history, and the Winchester 1895 certainly has one. Winchester sees it much the same way.
“The fact that we’re still producing the M95 is a huge testimony to the Winchester brand and the position it has in the marketplace,” Nielsen said. “Few companies get to claim they are still building the same guns that brought them to the table. If we can still build and sell a gun designed over 100 years ago, then we’re doing something right.”
You’ll get no argument from me on that score. I love the latest, greatest cartridges and gun designs we have available to us today—we’re living in a golden age, for sure—but there’s a lot to be said for a 125-year-old design and 116-year-old cartridge that are still ready, willing and able to continue to serve America’s hunters.
When the United States became actively involved in the First World War during the spring of 1917, our troops deployed to France soon found themselves in the unfamiliar environment of trench warfare. Since an important component of such fighting was periodic raids on enemy trenches, guns that were capable of being effectively wielded in close confines were particularly valuable. Handguns weren’t sufficiently powerful, and the standard Model of 1903 and Model of 1917 rifles were too long, cumbersome and slow- firing to be truly effective in such situations. Clearly, another type of arm was needed, but there was some debate as to just what it should be.
When deciding on what type of trench-fighting gun would be most efficacious, some senior Army officers, including Gen. John J. Pershing, then commander of the American Expeditionary Forces, remembered their experiences in the Philippines almost two decades earlier. When the United States gained possession of the Philippines from Spain following the Spanish-American War of 1898, our troops were faced with the unpleasant task of battling several indigenous groups who had fought the Spanish for decades and looked upon the Americans as just another occupying force.
Foremost among these were the fierce Moro tribesmen who exacted a deadly toll on American troops in close-quarters combat. The standardized .30-40 Krag rifles and .38 Long Colt revolvers proved to be unequal to the task, and a more effective arm was sorely needed. Circa 1900, the U.S. Army purchased some 200 of the newly introduced Winchester Model of 1897 short-barrel, slide-action shotguns for use in the ongoing “pacification” campaigns in the Philippines.
These “sawed-off” shotguns proved to be devastatingly effective close-quarters guns and were instrumental in eventually helping to quell the bloody uprisings.
Given the effectiveness of shotguns in the Philippines, it was recognized that a short-barrel, 12-ga. repeating shotgun loaded with 00 buckshot would also be a formidable tool in the trenches of France. It was decided to develop a shotgun specifically modified for trench warfare.
It was logical to base the new weapon on the tried and proven M1897 shotgun, but the War Dept. stipulated that the gun must be capable of mounting a bayonet. The M1897s previously used in the Philippines were standard commercial-production, plain-barrel “riot guns,” so a method of mounting a bayonet on the proposed shotgun had to be devised.
Working in conjunction with Springfield Armory, Winchester developed a metal one-piece bayonet adapter/handguard assembly. Since it would be necessary to grip the barrel to properly wield a bayonet-equipped shotgun, the assembly had a ventilated metal handguard for protection from a hot barrel.
The adapter was designed for use with the M1917 bayonet as used with the M1917 rifle. The new combat shotgun was soon dubbed the “trench gun,” although this was not official nomenclature. Production contracts were given to Winchester for the new firearm.
Since it was believed the new “trench gun” would be a valuable addition to our Doughboys’ arsenal, the Ordnance Dept. solicited proposals from other manufacturers for bayonet-equipped versions of their repeating shotguns. Remington Arms Co. submitted a “trench-gun” variant of its Model 10 slide-action repeating shotgun. Rather than the all-metal one-piece handguard/bayonet adapter used with the Winchester gun, the Remington Model 10 design featured a wooden handguard and separate bayonet lug, also adapted for the M1917 bayonet. The modified Remington Model 10 was adopted and put into production. The U.S. Army now had two standardized “trench guns,” but other models continued to be evaluated.
Although Remington had accepted large contracts for arms from other nations—chiefly Pattern 1914 rifles for Great Britain and M1891 Mosin-Nagant rifles for Russia— the company was still looking for additional business. Since the American government had adopted the Model 10 trench gun, the company believed that such guns might appeal to other nations but recognized that these potential purchasers likely wouldn’t be interested in a shotgun designed to use the U.S. M1917 rifle bayonet. Remington had a rather large number of “saber” bayonets for its No. 5 rolling-block rifles left over from previous South American contracts. The company submitted a standard Model 10 shotgun with a metal bayonet lug brazed to the underside of the barrel. However, no type of protective handguard was provided, which obviously limited the gun’s effectiveness in bayonet fighting. A prototype was submitted to the Ordnance Dept. for review, but little interest was shown, and it was rejected.
Undeterred, Remington turned its attention to the Russian government, which had placed large contracts for M1891 Mosin-Nagant rifles and bayonets. The Russian bayonet was an all-metal socket design with a cruciform blade. Having learned from the previous unsuccessful submission, the proposed “Russian trench gun” was equipped with a wooden handguard somewhat similar to that used on the U.S. Model 10 trench gun. The bayonet was locked into a metal flange and was not attached to the barrel as was the norm with most bayonets. Although it appeared to be a functional design, the fall of the Czarist government resulted in no real consideration being given to the gun, and it was discarded as well.
After these two abortive modified Model 10 prototypes, Remington came up with one of the most novel ideas for a trench gun ever conceived. A popular gun in the company’s product line was the semi-automatic Model 11 shotgun designed by the legendary John Moses Browning. It was believed that such a gun would be ideal for trench warfare due to its impressive rate of fire. There was, however, one major problem: The Model 11’s recoil-operated mechanism required that the barrel move back and forth with each shot. Since Ordnance specifications for trench guns mandated that they be equipped with a bayonet, Remington engineers had to devise some method of overcoming this inherent problem. Mounting a bayonet on the barrel wouldn’t be feasible because the added weight would not allow the barrel to reciprocate properly. Also, if a barrel-mounted bayonet was thrust into an adversary, the barrel would move backward and could, at least partially, eject a chambered shell, resulting in a jam.
The problem was ingeniously addressed by mounting a metal sleeve (tube) to the front of the receiver into which the barrel was fitted. A bayonet lug could be attached to the sleeve that didn’t affect the reciprocal movement of the barrel. In order to permit the gun to be properly grasped for bayonet fighting, a wooden fore-end that served as a handguard was fitted. There were at least two variations of the design that differed primarily in length with a slightly greater tubular magazine capacity for the longer pattern. It appeared to be a rugged and functional arm that likely would have been quite effective for its intended purpose.
The prototype Model 11 trench guns were completed by the fall of 1918, around the time of the Armistice. However, with the war ending, the Ordnance Dept. abandoned further consideration of the shotgun. The prototypes were shelved, and, perhaps surprisingly, the concept was never revisited. It is intriguing to think that if the gun had been available a year or so earlier, it might have been adopted. As events transpired, even though the Model 11 trench gun never made it past the prototype stage, large numbers of plain-barrel Model 11 riot guns (and long-barrel training guns) subsequently saw service during World War II.
In addition to the Remington designs, there was another proposed trench gun fabricated and submitted for testing in 1918. The J. Stevens Arms and Tool Co. developed a trench gun based on its Model 520 slide-action shotgun. Rather than using a wooden handguard, like the Remington guns, or a one-piece metal handguard/bayonet adapter assembly, like Winchester, Stevens equipped its gun with a ventilated metal handguard and a separate bayonet lug on the barrel. The shotgun reportedly acquitted itself quite well in testing, and it is speculated that a small number may have been purchased, but this is unconfirmed. Unfortunately for Stevens, like the Remington Model 11 prototypes, the end of the war resulted in the cancellation of all pending contracts. Stevens had better luck with a trench-gun version of the Model 520-30 (an improved 520) during World War II when substantial numbers were procured and issued along with some Stevens M620A trench guns.
If the First World War had lasted into 1919 as had been expected, it is possible that at least two additional trench guns, the Remington Model 11 and Stevens 520, could have found their way into the trenches. Instead, the only two trench guns to be issued during the war were the Winchester M1897 and the Remington Model 10. Nevertheless, the efforts to develop innovative designs for a new type of combat arm, the “trench gun,” illustrate the resourcefulness and expertise of American gunmakers at a critical time in our history.